Oxetane
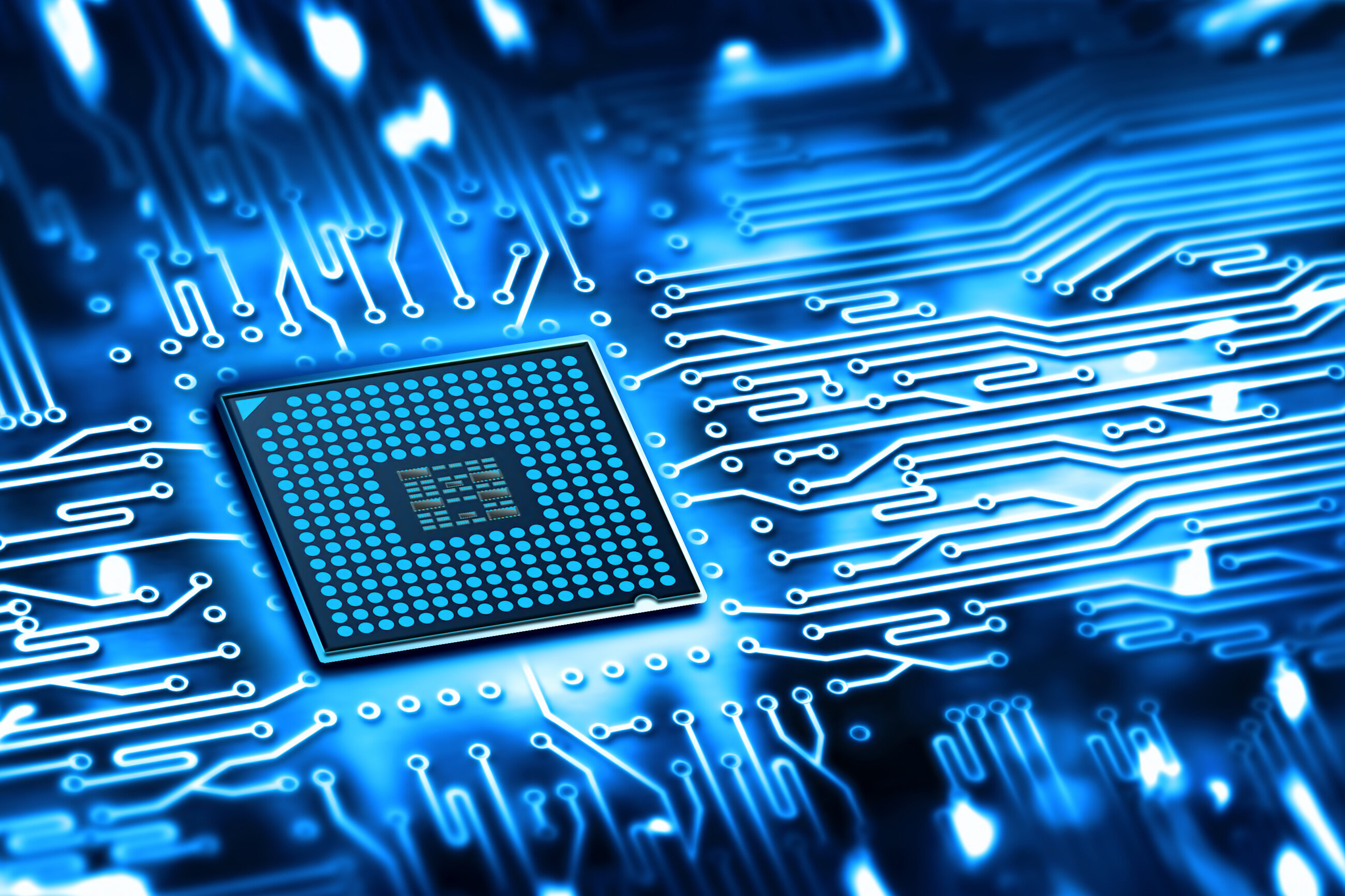
This is a cationic curable additive for epoxy resin characterized by its quick curing of epoxy resin, shrinkage control and strong adherence to plastic materials.
- Product Name
-
ARON OXETANE
Catalog
Trade name | Common Name | Main Structural formula | Viscosity (mPa-s) 25°C | Tg (℃) |
Features | TDS |
---|---|---|---|---|---|---|
OXT-101 | 3-Ethyl-3-hydroxymethyl-oxetane |
![]() |
17-22 | 46 |
|
|
OXT-211 (under development) | 3-Ethyl-3-(phenoxymethyl)oxetane |
![]() |
10-20 | 1 |
|
|
OXT-213 (under development) | 3-Ethyl-3-(cyclohexyloxy)methyloxetane |
![]() |
3-12 | 1 |
|
|
OXT-212 | 3-Ethyl-3-(2-ethylhexyloxymethyl)oxetane |
![]() |
3-6 | -60 |
|
|
OXT-121 | 1,4-Bis{[( 3-ethyloxetan-3-yl)methoxy]methyl}benzene (main component) |
![]() |
150-185 | 94 |
|
|
OXT-221 | 3-Ethyl-3-{[[(3-ethyloxetan-3-yl)methoxy]methyl}oxetane |
![]() |
9-14 | 51 |
|
|
OXT-191 | Oxetanil Silicate |
![]() |
3,000-10,000 | - |
|
* OXT-211, 213 : Development product
Features
Features of ARON OXETANE
1. Quick curing of epoxy resin
Epoxy resin generally exhibits a fast reaction initiation but slow propagation, and yields only oligomers at around several thousands in molecular weight. Therefore, it only gives rise to hard and brittle molecules. On the other hand, oxetane resin has a slow start and does not begin to polymerize even when exposed to light. However, once the concentration of the radical initiator reaches a certain level, polymerization happens at a high speed to give rise to polymers of tens of thousands in molecular weight.
When epoxy resin is combined with oxetane resin in such a way that makes the most of their respective characteristics, it is possible to overcome their individual shortcomings. In other words, when epoxy resin with quick initiation is added to oxetane resin, the curing speed may be equivalent or superior to that of the cycloaliphatic epoxy used for light cationic polymerization. As the added epoxy increases, even though the molecular weight of the resulting polymer is slightly less than in the case of using oxetane resin alone, it is sufficient as a high polymer and therefore it is possible to design cured substances with extensibility and toughness.
As the reactivity of epoxy resin is not accelerated by mixing with oxetane resin, a large amount of oxetane resin is required in a mix when rapid curing is needed.
2. Dark reaction (post-polymerization)
Cationic curable resin is characterized by the fact that polymerization continues even after exposure to ultraviolet light. Normally, it takes four hours for cycloaliphatic epoxy resin to cure to exhibit solvent resistance. Oxetane resin is fairly reactive, such that its post-curing is rapid. Within an appropriate system, it yields adequate performance after around ten minutes of ultraviolet irradiation.
3. Impact on physical properties through addition in small quantity
The physical properties of the cured product will change even with a small amount of oxetane resin added. The Tg of UV-cured product can be raised by 10℃ through adding 10-20% of highly reactive oxetane resin. This is believed to be due to the rising temperature of the chemical system as a result of the heat of reaction of the small amount of oxetane resin. In addition, the addition of a small amount of oxetane resin also enhances the breaking strength.
4. Adhesion
In most cases, the addition of oxetane resin lowers the adhesive strength. Since oxetane resin is highly reactive, the stress caused by curing shrinkage is believed to be concentrated in the interface due to a small amount of hydroxyl group forming from the initiator and a short reaction time. Particularly, if the adherend is made of plastic, it is necessary to lower the curing speed or to blend a material with high wettability into the adherend. Effective methods of increasing adhesiveness include adding a high molecular weight resin or glycidyl ether epoxy resin to control the reaction speed, and using heated aging to eliminate internal stress.
5. Mixing with glycidyl ether epoxy resin
Monofunctional and bifunctional oxetane resins have very low viscosity and make it possible to blend a larger amount of high viscosity resin to extend the range of mixing formulas. In addition, with the high reactivity of oxetane resin, it is possible to blend with materials for cationic polymerization that would otherwise have poor reactivity, such as glycidyl ether epoxy resin, including bisphenol-A type and novolac type resin, or epoxy modified butadiene and other resins marketed as epoxy modified polymer. This is one of the most effective blending solutions for producing adhesives and sealing agents.
6. Storage stability
For most materials composed solely of epoxy resin, the molecular weight and perceived viscosity do not increase even after a small amount of acid is generated from initiators over time. On the other hand, systems containing oxetane resin in the blend generate high molecular weight polymer and increased viscosity. In such cases, it is necessary to use a different initiator with higher stability or to add a stabilizer.
7. Impact of moisture
Ultraviolet cationic curing is considered to be affected by moisture. While in most scenarios, there is no significant reaction inhibition with water being added to a mixture, atmospheric moisture exerts a significant impact. Generally, oxetane resin is more sensitive to water than epoxy resin, but it can be used in a stable state if the atmospheric humidity can be controlled.
Usage
Usage of UV-curable resins
1. For use as UV-curable materials (ARONIX and ARON OXETANE)
UV-curable resins undergo polymerization as the initiator produces radicals and cations with exposure to light. Given the advantage of this reaction, UV-curable resins are used in a wide range of fields.
Generally speaking, the use of UV-curable resins can minimize the amount of solvent use, thereby making it possible to design products that are earth and work environment friendly. There are also other advantages as follows.
- Rapid curing time
The short curing time increases production and energy efficiency (energy saving), reduces space, and makes it possible for use on non-heat resistant materials.
- Easily controlled curing process
Since the reaction only takes place in areas exposed to light, it is possible to control the reaction through masking or similar means to allow only the required parts to react.
The speed of light curing of ARON OXETANE alone is not particularly high. Blending with epoxy resin prior to light curing drastically improves the speed of light curing and the properties of the cured products.
- 1-1. Light curable inks and paints
Light (ultraviolet light) curable inks, characterized by their high curing speed, have been in practical use since around 1970 for sheet-fed printing and web offset printing. Lately, their applications have expanded to gravure inks and inkjet inks. They are indispensable as materials for a range of resist inks that take advantage of their image forming properties.
Light (ultraviolet light) curable paints are widely used as protective coatings and hard coatings for paper, wood, plastics, and metals, and in everyday products, including beverage cans, fiber optic materials, and mobile phones. - 1-2. Electron beam curable paints
Radical polymerization is a method of curing the coating surface using an electron beam. As it does not involve the use of light initiators, it can be used for materials impenetrable to light including metallic films and high-concentration pigments. While this method also increases adhesiveness, it is subject to severe equipment limitations and has yet to find widespread application.
- 1-3. Light-curable adhesives
As with other adhesives, light-curable adhesives exert their adhesive functions by forming polymers and hardening through polymerization reactions. They are characterized by the chain polymerization reactions triggered by irradiation with light. Moreover, they require no mixing of two solutions, offer flexibility in set time, as well as possess excellent storage stability. Their use in the field of data recording media, such as DVDs, has become more in demand in recent years.
- 1-4. Resist materials
These are used in both etching and solder resists. Materials that contain carboxylic acids are used to produce alkaline developing ability. The use of resist materials in LCD color filters has increased in recent years.
They are also used in press plates for flexographic printing, such as for newspaper printing.
2. Epoxy resin modification (ARONIX, ARON OXETANE)
- 2-1. Improvement of light-curable epoxy resin curing performance (ARON OXETANE)
This is the biggest feature of ARON OXETANE. The combination of light-curable epoxy resin, which has quick initiation, slow propagation, and difficulty achieving a high molecular weight, with ARON OXETANE, which is characterized by slow initiation and rapid polymerization once the initiating radicals reach a certain concentration to form high molecular weight material with extensibility and toughness, makes it possible to deliver rapid curing and polymerized material with a high molecular weight for improved heat and alkali resistance.
Specifications
ARON OXETANE curing methods
Cationic ring-opening polymerization with acid is the typical curing method of ARON OXETANE.
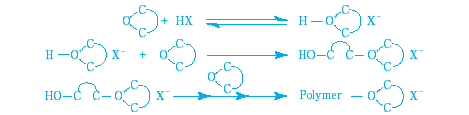
Typical curing methods of ARON OXETANE are as follows. As oxetane resin by itself has a slow reaction initiation, we recommend addition of epoxy resins.
Curing methods | Example of catalyst system | |
---|---|---|
Cationic polymerization | Heat-curing | Add heat initiator (trialkyl sulfonium salt, triaryl sulfonium salt) |
UV-curing | Add UV-initiator (triaryl sulfonium salt, diaryliodonium salt) |
World of UV-curable resins (area of Toagosei's commercialization)
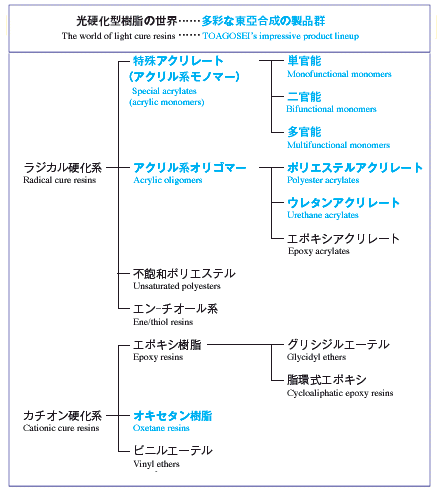
We offer many other products under the ARONIX brand not included in the catalog.
In addition, we also welcome inquiries regarding design and development of new products according to customer needs, dilution with solvents, mixing of multiple brands, as well as compound product design and supply (ARONIX UV series). Please contact us.
Overseas expansions
Toagosei manufactures ARONIX at its Nagoya Plant as the main site of production. For overseas locations, we established a sales location in Taiwan in 2000 (TAIWAN TOAGOSEI Co., Ltd.) and a began manufacturing in 2001 (TOA-JET CHEMICAL Co., Ltd.). Furthermore, we established a new company in Zhangjiagang, Jiangsu, China in 2004 (TOAGOSEI (Zhangjiagang) New Technology Co., Ltd.) to conduct manufacturing and sales, which began operations in 2005. With the projected growth in demand in the Asian Market, we aim to expand worldwide starting from Asia.
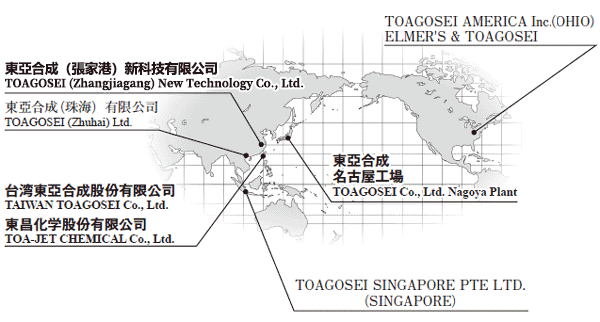
Cautions when handling UV-curable resins
ARONIX and ARON OXETANE are for industrial use. Consult the product safety data sheet (SDS) to ensure you understand the risks and take proper health and safety measures and environmental measures.
Contact us if you have any questions.
- Exposure of ARONIX, special acrylic monomer and oligomer product, to the skin, eyes, or mucous membranes may trigger rashes, inflammation, and allergic reactions.
1. Ensure proper ventilation
Generally, it has a high boiling point and low volatility, therefore there is almost no damage to the skin caused by steam at room temperature. However, steam may occur during heating or UV-curing. Ensure proper ventilation in the work space.
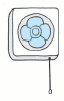
2. Wear appropriate protective equipment
- Wear protective equipment such as gloves, apron, and safety goggles to avoid contact of the substance with the skin, and do not handle with bare hands.
- If wearing protective gloves, make sure the contaminated gloves do not touch the skin.
- Natural rubber is an effective material for the protective gloves. Vinyl gloves may allow the material to penetrate and are not suitable.
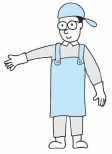
3. Promptly rinse under water if the product comes in contact with the skin.
Be very careful of skin contact as the liquid is clear and does not cause irritation when initially exposed to the skin.
Rinse with soap water immediately as long term contact with skin can cause skin damage.
Avoid washing with solvents, as they will speed up penetration of the material into the skin. In case of skin contact, inhalation or ingestion of the material, seek medical attention and treatment even without subjective symptoms.
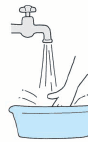
4. If the product gets in contact with the eyes, immediately rinse with plenty of water for at least 15 minutes and seek medical attention from an ophthalmologist.
5. If inhaled, relocate to a place with fresh air to rest and seek medical attention immediately.
6. Seek medical attention immediately if ingested. Keep away from heat, sparks, open flames and other sources of ignition. In the event of a fire, wear protective equipment (and a respirator if necessary) to extinguish the fire from upwind using powder, foam or carbon dioxide fire extinguisher.
- This is an inflammable and flammable substance. Keep away from heat, sparks, open flames and other sources of ignition.
In the event of a fire, wear protective equipment (and a respirator if necessary) to extinguish the fire from upwind using powder, foam or carbon dioxide fire extinguisher. - As a highly reactive substance, polymerization will occur as a result of exposure to light, impact, heat, and mixing with other substances, which can lead to sudden heating, damage and breakage of containers.Use upon confirming the reactivity in advance.
- In case of a spill from the container, remove sources of heat and ignition from its surrounding, and use paper towel or sand and gravel to recover the spillage in an empty container if the amount is small, then rinse the area with plenty of water. If there is a large amount of spill, enclose it in embankment to stop the outflow and collect it in a closed container. Handle while wearing protective equipment.
- Contact a waste material processor for disposal.
7. Primary skin irritation
The report by Huntingdon Life Sciences Ltd. (former Huntingdon Research Center UK) has assigned the following ranks, with P.I.I. as follows. Generally, they are considered hypoallergenic.
P.I.I. | Categories |
---|---|
0 | Non-irritant |
> 0 - 2 | Mild irritant |
> 2 - 5 | Moderate irritant |
> 5 - 6 | Moderate to severe irritant |
> 6 | Severe irritant |
The P.I.I. of ARONIX and ARON OXETANE are published in the list of grades.
8. Storage method
Store following the regulations stipulated by applicable laws and regulations such as the Fire Service Act.
- Avoid hot objects, sparks and open flames, and do not store in the same place as oxidizing materials and peroxides.
- Store well sealed in a well ventilated, cool, and dark location (30℃ or under) and avoid direct sunlight.
- Keep electrical equipment in the storage location in an explosion-proof structure, and ground the equipment.
- Do not transfer to other containers.
Related product
Inquiries
- Department in charge
- POLYMER & OLIGOMER DIVISION OLIGOMER DEPARTMENT
- Phone number
- +81-3-3597-7332
*9:00 am - 5:00 pm (except weekends and holidays)